Sandy Alexander installs “flagship” Heidelberg Speedmaster XL 106 at Clifton location
Aug 9, 2021
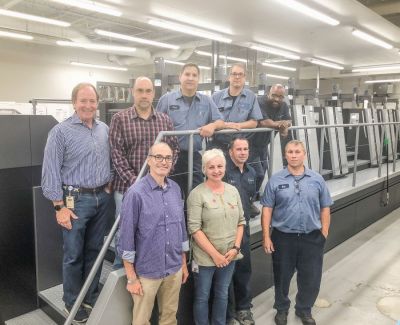
KENNESAW, Georgia – Sandy Alexander, a nationwide provider of integrated multi-channel graphic communication solutions, has installed a new Speedmaster XL 106-8P with Push-to-Stop technology from Heidelberg at its Clifton, New Jersey, headquarters. The press, which is Heidelberg’s newest generation of Speedmaster machines, demonstrates Sandy Alexander’s continual commitment to providing the most technologically advanced solutions for its customers.
THE 'BEST' MACHINE FOR ITS CLIENTS
Despite the challenges that COVID-19 brought upon much of the printing industry, Sandy Alexander set a firm focus on its future when it began investigating new offset press options in 2020.
“In good times and bad, we are committed to investing heavily in the company and in our customers,” Mike Graff, CEO & president of Sandy Alexander, said.
This commitment is in part why the 55-year-old company was recently ranked #37 on Printing Impressions Top 350 list and why it has retained some clients for as many as 35 years.
Providing the best for its clients is also why Sandy Alexander selected the latest generation Speedmaster XL 106-8P for its newest investment. The new XL 106, which replaces an aging machine in the company’s Clifton facility, will be the “flagship” press for Sandy Alexander, who hopes to shift much of the offset work it produces for its high-end cosmetics, fashion, automotive, travel and entertainment, and restaurant clientele onto the machine.
According to Graff, “Sandy Alexander has always ensured that it has the best equipment available. We look to Heidelberg as the leader in technology and high-quality print. We truly believe that this is the best machine out there.”
The new XL 106 features the most advanced offset technology available on the market today. This includes Heidelberg’s Push-to-Stop autonomous manufacturing approach – driven by Intellistart, a unique integrated software system that greatly reduces the number of operating steps during a job change, and AutoPlate Pro, a fully automatic plate change system that controls precise plate feeding for exact and fast registration at the start of each job.
“As with all of our investments, our goal is to enhance our customer experience. By better automating our processes, our team will be able to better focus on productivity and eliminating unnecessary waste and downtime. Through these efforts, we can make print more cost effective for our customers,” Graff said.
The new investment, which also includes installing Prinect Production Manager, is the first step that Sandy Alexander is taking to achieve a complete closed loop JDF workflow from prepress to bindery. With Production Manager, job files and presetting data are sent to the press directly, which greatly automates the press set-up and decreases makeready time. With full automation from prepress to press, Sandy Alexander is anticipating increasing its overall capacity and throughput – eventually looking downstream to extend automation into its bindery in the near future.
In addition to Heidelberg’s advanced technology, Graff cites Heidelberg’s commitment to building reliable products and “robust” service offerings as other reasons why the XL 106 is the best fit for Sandy Alexander. “Having had previous Heidelberg presses in the past, we know that with our latest investment, the longevity of this machine is going to give us a great return on our investment.”
About Sandy Alexander
Through the years, Sandy Alexander has grown because of a long term symbiotic strategic partnership with its clients. This relationship was built on a foundation of best practices in printing and a commitment to servicing all of the communication needs of its clients. The result is a diverse company that was born out of printing but has evolved into a multi-platform, multi-channel marketing communications company with capabilities ranging from CG studio services, digital printing, direct mailing, data driven marketing solutions, and retail visual merchandising. The company’s success has been the result of four guiding principles: providing a single source for its clients, color science management, marketing technology solutions, and sustainable intelligence.